Así se fabrica una batería de coche eléctrico en una gigafactoría
Las baterías se han convertido en el elemento de moda en la industria automotriz, ya que son la clave del éxito del coche eléctrico, tanto a nivel de prestaciones como de sostenibilidad y costes. Te contamos cómo es el proceso de fabricación de cada unidad.
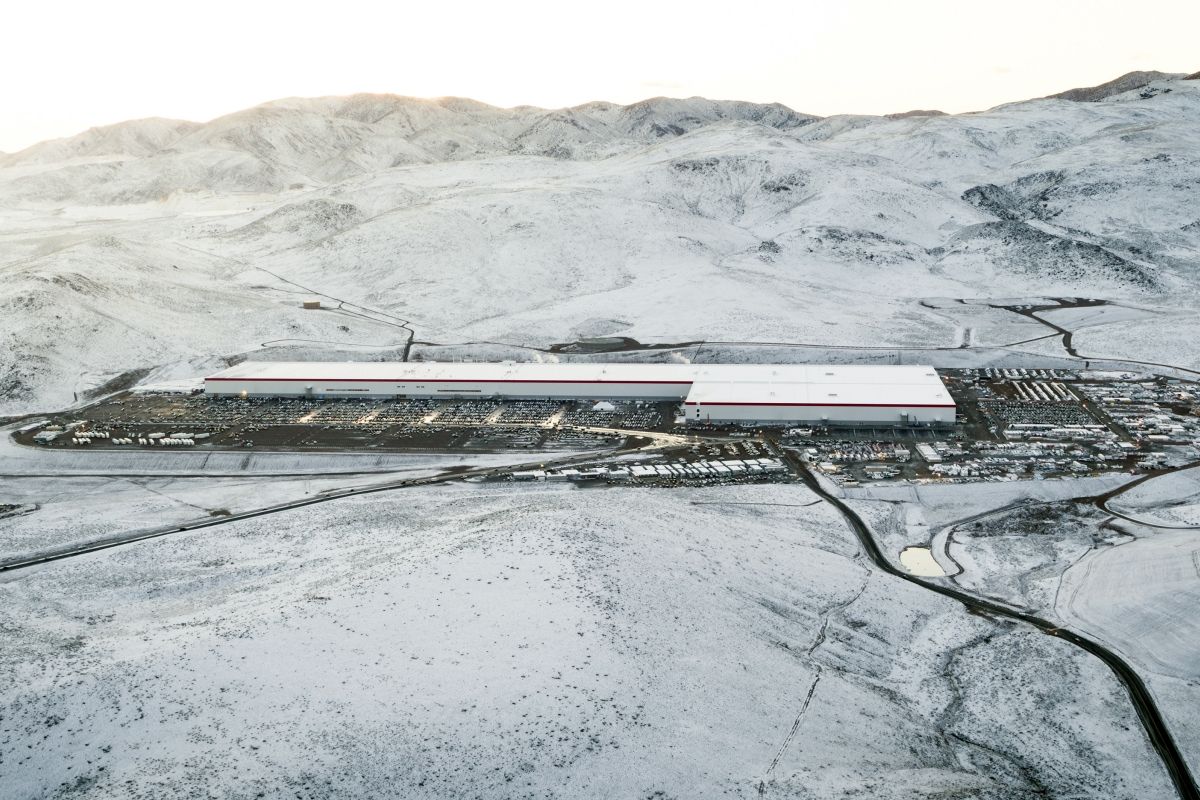
La proliferación de las gigafactorías se ha convertido en uno de los temas estrella de la actualidad informativa relativa al sector del automóvil.
Cada vez son más las instalaciones que tanto empresas independientes como fabricantes de vehículos ponen en marcha y, no en vano, sólo en 2022 se pusieron en marcha 102 gigafactorías en todo el mundo.
Para evitar contaminaciones entre materiales, el ánodo y el cátodo se constituyen en líneas de fabricación independientes
Y, como podrás imaginar, el proceso de elaboración de una batería es sumamente complejo. Actualmente, este se realiza recurriendo a procedimientos digitalizados y automatizados que permiten, no sólo un alto control de calidad, sino también una notable eficiencia y reducción de costes.
Podemos resumir el proceso de fabricación de una batería en tres grandes fases: la fabricación de los electrodos, el ensamblado de las celdas y, finalmente, la formación y validación del funcionamiento de las baterías. Cada uno de estos procesos está formado por muchos otros que veremos a continuación.
Fabricación de electrodos
Los electrodos de una batería, denominados cátodo y ánodo, protagonizan el primer paso de elaboración de una batería.
Para evitar contaminaciones entre materiales, uno y otro se constituyen en líneas de fabricación independientes. Generalmente, el ánodo se compone de una lámina de cobre recubierta de grafito, mientras que el cátodo está formado por una lámina de aluminio que, eso sí, puede estar recubierta de muchos compuestos químicos diferentes, en función del tipo de batería que se quiera obtener.
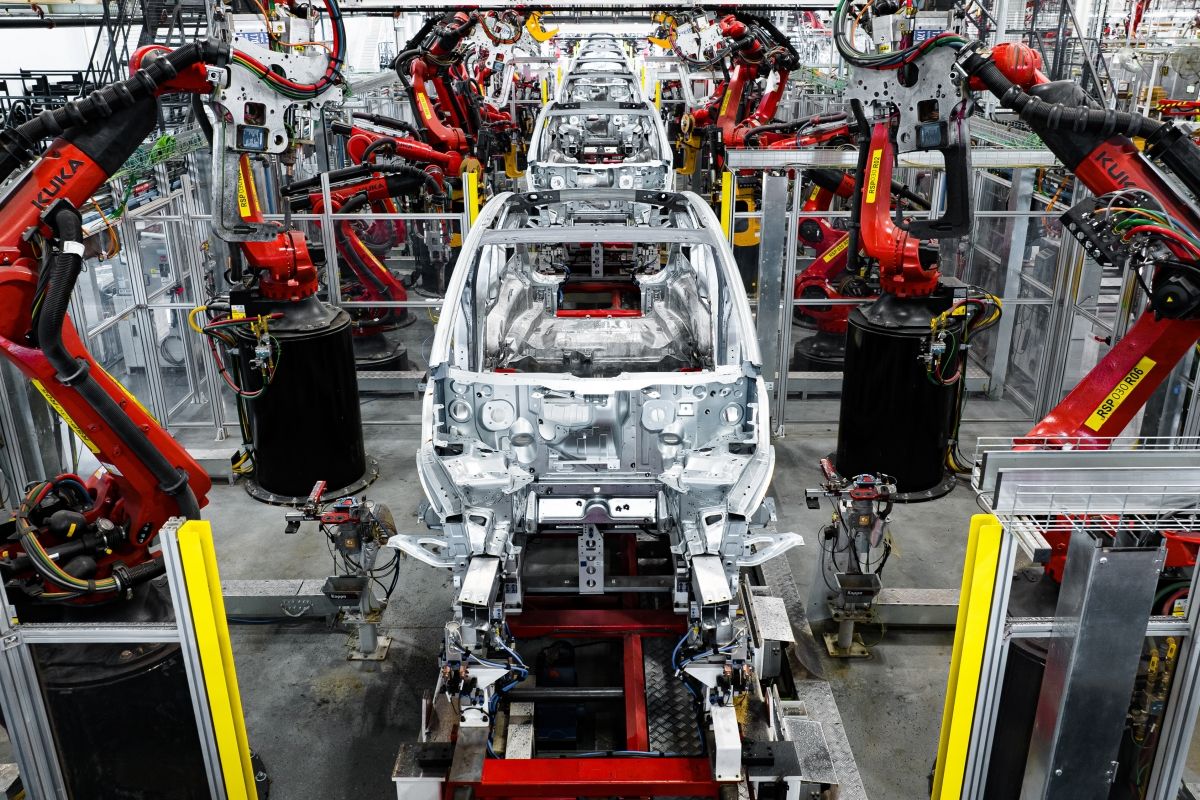
Mezcla
Este proceso consiste en elaborar lo que se conoce como «slurry», que es una mezcla de polvos, disolvente y aglutinante para crear una masa pastosa.
Para hacerlo, se utilizan equipos de producción en lote (generalmente mezcladores planetarios) o equipos de producción continua (operaciones básicas de dosificación a lo largo de la cámara de mezclado mediante alimentación gravimétrica automática).
Recubrimiento y secado
La masa pastosa resultante de la mezcla se introduce en tuberías que la llevan a la zona de imprimación. Allí, dicha masa se imprime sobre un sustrato o bobina metálica.
Este sustrato o bobina pasa a un horno de secado, que evapora el disolvente y deja los polvos anteriormente mencionados adheridos a la lámina de manera uniforme. Esta operación debe realizarse de manera gradual para obtener así un electrodo de buena calidad.
El recubrimiento se aplica sobre las dos caras del sustrato o bobina, y puede ser intermitente o continuo. Esto vendrá definido por el formato y tamaño de la celda de la batería en la que se vaya a introducir posteriormente.
Calandrado
Así es como se denomina el proceso de acabado del sustrato o bobina recubierta. Estos elementos se hacen pasar por dos rodillos calentados para comprimir el material, asegurando de ese modo una mejor adherencia, un espesor constante y una densidad conforme a las necesidades.
Corte
En este último paso, se cortan las bobinas para crear los electrodos individuales. Para ello, las bobinas se pasan por un banco de cuchillas formateadas para ajustarse al diseño deseado.
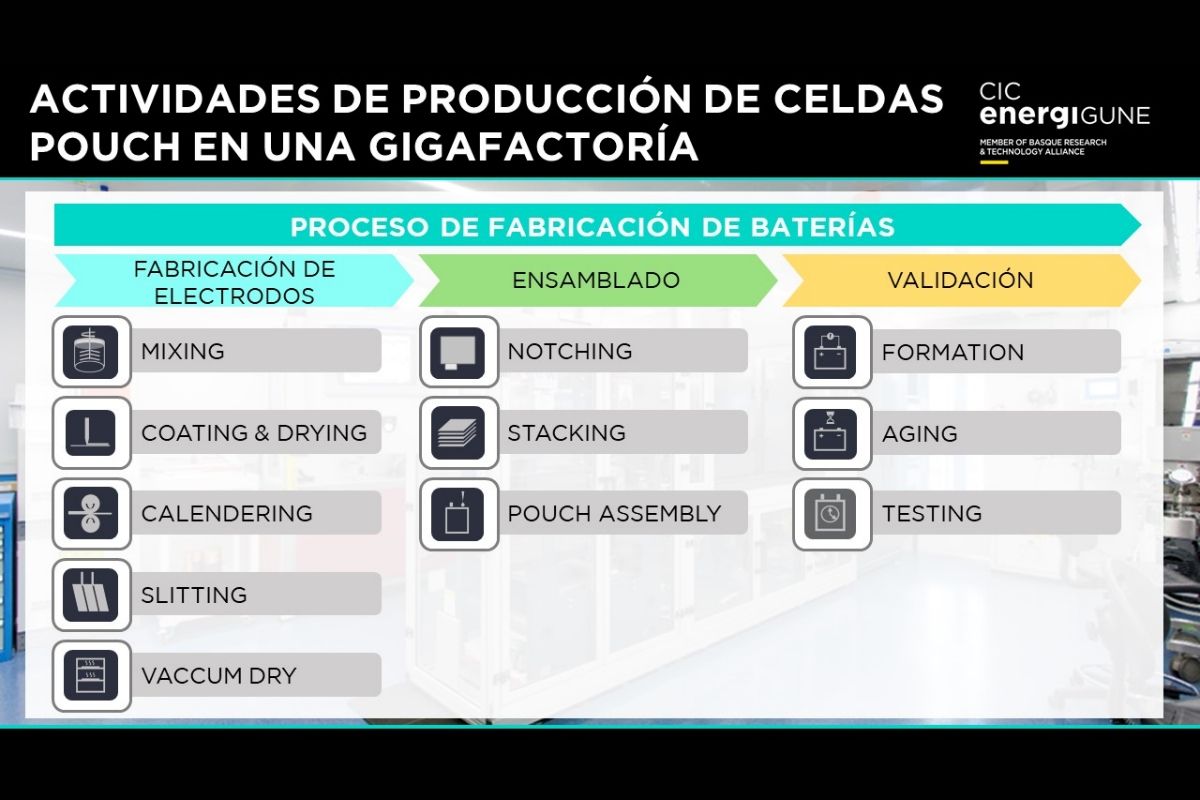
Ensamblado de las celdas
Los electrodos ya están fabricados y ahora es el momento de ensamblar las celdas de las baterías.
Esto debe hacerse en un ambiente seco para evitar la penetración de humedad en el electrodo. Si no fuera así, este perdería capacidad, se degradaría más rápidamente o incluso podría formar ácido fluorhídrico.
Para evitarlo, los electrodos pasan por hornos de vacío y se trasladan a un entorno controlado denominado «sala seca» para garantizar la calidad de las celdas. En ella, la temperatura suele ser de - 40 ºC (punto de rocío), aunque con la proliferación de químicas más sensibles se están haciendo necesarias temperaturas incluso más bajas.
En esta fase, los electrodos se cortan a la medida exacta y se ensamblan en sus carcasas, si bien el tipo de celda determina el proceso a seguir. Poniendo como ejemplo las baterías tipo pouch, se diferencian tres grandes pasos en este proceso:
- Notching: produce electrodos rectangulares con pestañas mediante corte mecánico o láser.
- Stacking: se produce el apilamiento de las celdas, combinándose por primera vez las líneas de producción de ánodo y cátodo. El propósito es apilar de forma alternativa capas de ánodo, separador y cátodo, pero dejando al descubierto las pestañas.
- Ensamblaje: se unen las pestañas a los terminales mediante soldadura. Posteriormente, la celda se inserta en su material de embalaje dejando un borde abierto. Luego, se rellena con electrolito y se sella al vacío.
El producto de todo ello se deja en remojo durante horas antes de ser enviado al siguiente paso de fabricación de la batería.
Formación, envejecimiento y validación
La batería ya ha sido ensamblada, pero aún debe acondicionarse. Esta última fase es crítica para el buen funcionamiento de la misma.
Lo primero que se hace es una carga inicial de la celda, evaluándose a continuación sus características y rendimiento.
Luego, se acometen los procesos de precarga, desgasificación, formación, envejecimiento a altas temperaturas, etc, que diferirán en tiempo y forma en función del tipo y calidad de la batería. De hecho, este proceso puede incluso durar semanas.
Una vez completada esta última fase, la batería final ya ha sido obtenida y está lista para su uso
Breve recorrido por una gigafactoría de CATL, el mayor fabricante de baterías del mundo.
Queda claro, por tanto, que el proceso de fabricación de una batería exige un nivel de precisión y complejidad que explica el alto coste de elaboración de las mismas. En el futuro, la reducción de costes pasará seguramente por la implementación de materias primas menos costosas que, a su vez, permitan procesos más sencillos.
Además, muchos fabricantes han comenzado a basar sus instalaciones en Machine Learning e Inteligencia Artificial para optimizar y mejorar continuamente los procesos.
Todo ello tendrá que evolucionar también con la sostenibilidad y un reciclaje eficaz en mente, ya que de lo contrario el objetivo final de la electrificación del transporte y la industria no podrá cumplirse.
Fuente: CIC energiGUNE