Bugatti fabrica la primera pinza de freno del mundo con titanio y en impresión 3D
Bugatti fabrica una pinza de freno con ocho pistones para el deportivo Chiron utilizando la avanzada impresión 3D, el primero en utilizar esta técnica y en usar titanio, una tecnología que abre nuevas posibilidades en la industria y una prueba piloto antes de implementarla en los procesos de producción a partir de este año.
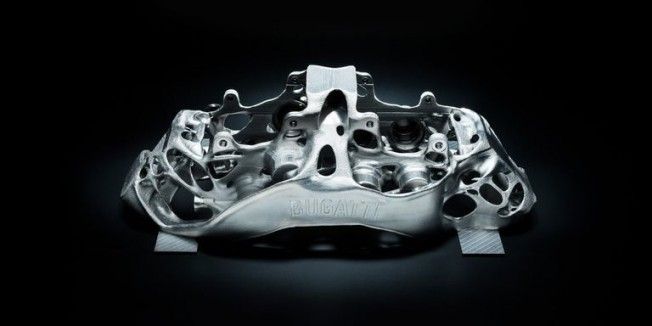
Detalle de la primera pinza de freno del mundo fabricada por Bugatti utilizando titanio y en una impresora tridimensional
Bugatti avanza en materia de desarrollo presentando la primera pinza de freno del mundo fabricada en titanio con tecnología de impresión tridimensional, dos hitos que integrará en los procesos de producción de sus modelos a partir de la primera mitad de este año.
Hasta ahora, la fabricación de este componente se veía realizando en hierro o en aluminio, pero nunca con titanio lo que abre también nuevas posibilidades en el uso de este material aunque el fabricante francés matiza que el tratamiento especial del material requiere una impresora -la más grande mundo que se encuentra en Alemania- equipada con cuatro láseres de 400 vatios.
Bugatti afirma que ha utilizado una aleación especial usada en la industria aeroespacial y que ofrece un rendimiento considerablemente más alto que el aluminio, capaz de soportar una fuerza de poco más de 125 kilogramos a un milímetro cuadrado de esta aleación de titanio sin que se rompa el material. Además, la nueva pinza de freno de titanio comparada con las de aluminio que monta el deportivo francés sólo pesan 2,9 kilogramos, por lo que los cálculos de los ingenieros de la firma estiman una reducción de peso del 40 por ciento ofreciendo mayor resistencia.
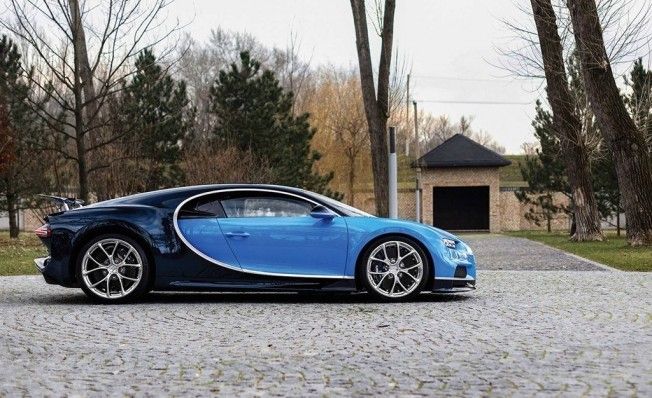
El Bugatti Chiron será el modelo que estrenará las primeras pinzas de freno de titanio realizadas en una impresora 3D
Frank Götzke, Jefe de Nuevas Tecnologías en el Departamento de Desarrollo Técnico de Bugatti apunta que "el desarrollo de un vehículo es un proceso interminable, y particularmente cierto en Bugatti, ya que en nuestros continuos esfuerzos de desarrollo, siempre estamos considerando cómo se pueden utilizar nuevos materiales y procesos para mejorar aún más el Chiron y cómo se podrían diseñar futuros vehículos de nuestra marca", añadiendo que "como nuestros datos de rendimiento a menudo están en los límites físicos, somos especialmente exigentes y la razón por la que Bugatti siempre va un paso más allá que otros fabricantes en el desarrollo de soluciones técnicas".
Götzke señala que el desarrollo de la nueva pinza sólo ha requerido tres meses, desde su concepción y cálculos necesarios hasta la impresión, un proceso que necesita de 45 horas para que el polvo de titanio se deposite en 2.213 capas -con variaciones entre uno y cuatro milímetros entre las capas- y que los cuatro láseres lo fundan en la forma definida de la pinza de freno. Un tratamiento térmico estabilizador aplicado sobre la pieza alcanza su resistencia final con una temperatura inicial de 700° C que cae a 100° C para eliminar la tensión residual y garantizar la estabilidad dimensional.
Pero, al mismo tiempo que el fabricante confirma que se trata del primer componente de titanio del mundo, no es la primera vez que utilizan la tecnología de impresión 3D anunciando que lo han hecho antes con aluminio; concretamente, en un parabrisas de 63 centímetros de largo y que sólo pesa 400 gramos, la mitad del peso de una lámina de aluminio ligero fundida a presión sin perder ni un ápice de rigidez.
Bugatti ha confirmado también que van a comenzar a montar estas nuevas pinzas en unidades del Chironpara realizar pruebas en esta primera mitad del año prometiendo que esta nueva técnica de fabricación permitirá reducir significativamente los tiempos de producción.
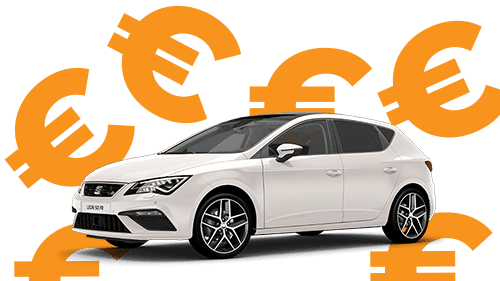