Técnica F1Así funciona el taller de mecanizado de McLaren
El túnel de viento o el departamento de simulación por ordenador suelen llevarse la mayor parte de la atención, pero en todo equipo de Fórmula 1 existe un lugar clave para el éxito. El taller de maquinaria y mecanizado constituye una pieza clave en el entramado de una factoría en el que se construyen cerca de 3.000 piezas semanales y se trabaja con titanio, aluminioy acero inoxidable.
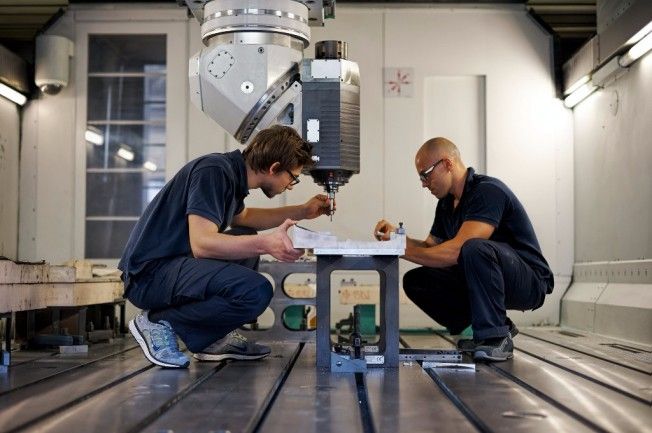
Cuando piensas en un coche de Fórmula 1, invariablemente piensas en una máquina que está hecha casi enteramente de fibra de carbono. Pero esa es sólo una parte de la historia. Si bien la fibra de carbono ha sido adecuadamente reconocido como el maravilloso material que ha permitido a la F1 construir coches más seguros, sofisticados y rápidos, es sólo uno de los muchos materiales utilizados por los equipos.
El taller de maquinaria pesada que cada equipo tiene en su factoría se encuentra poblado por una selecta gama de maquinaria que trabaja principalmente con titanio, aluminio y acero inoxidable. ¿Por qué? porque en ocasiones los componentes de fibra de carbono no ofrecen la mejor solución y una pieza de metal adecuadamente mecanizada sí.
McLaren utiliza titanio porque la relación entre resistencia y peso lo convierte en un material extremadamente versátil. El aluminio es más pesado, pero relativamente ligero y muy resistente. El acero inoxidable es notablemente más pesado, pero tiene una resistencia al desgaste y una fortaleza increíbles.
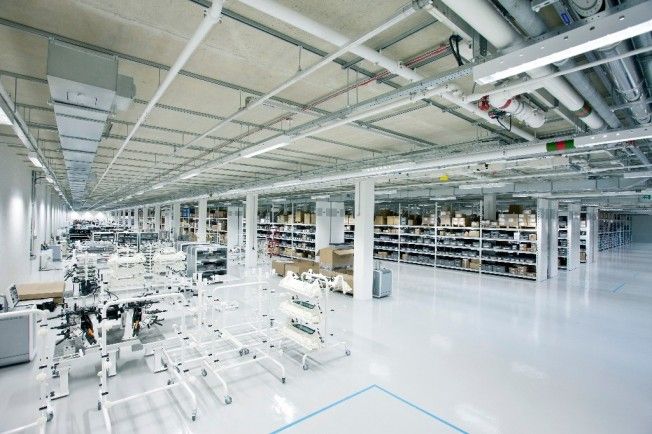
Como siempre, el propósito del componente dicta el material a utilizar. Incluso en un deporte en el que la fibra de carbono es tan frecuente, el taller de mecanizado se mantiene particularmente ocupado durante los meses de invierno cuando todo el equipo se centra en la construcción de los monoplazas de cada temporada.
Sentirse como nuevo
“Este invierno ha sido particularmente intenso”, reconoce el mecánico de McLaren Malcolm Jones. “Para el MCL32, cada pieza mecanizada del coche ha sido cambiada para esta temporada. En un invierno normal, esperamos que alrededor del 70 u 80% de las piezas sean nuevas, pero en esta ocasión es el 100%. Ello se debe al nuevo reglamento de la Fórmula 1 que hacen que los coches sean completamente distintos. Todo es más grande o más largo”.
El nuevo reglamento ha creado reverberaciones sísmicas en la fábrica. De repente todo lo que no requería un cambio ha tenido que ser rediseñado. Tratemos de imaginar cuánto cuesta, por ejemplo, rediseñar y construir 150 carros de neumáticos para el transporte por todo el mundo o pedir 160 mantas térmicas nuevas, simplemente porque las dimensiones de los neumáticos han cambiado considerablemente.
“Es un reto”, admite Malcolm. “Para este año, todas las estructuras principales y las suspensiones son diferentes y eso afecta al ritmo de trabajo. El taller de mecanizado realiza piezas para el túnel de viento al 50% del tamaño original, así que ese es el primer indicativo de que hemos afrontado varios retos este invierno. Todo es un poco menos sencillo, ¡pero adoramos los retos!”.
Cuando la temporada anterior termina, el programa de construcción del coche se intensifica con todos los recursos de la factoría centrados en el diseño y construcción del nuevo chasis. En el taller de mecanizado, la demanda de piezas nunca ha sido mayor: “En la primera semana de febrero, llegamos a nuestro máximo nivel”, dice Jones. “Completamos más de 560 procesos de fabricación y cada proceso puede consistir en un pedido de cinco o seis piezas, por lo que potencialmente fabricamos alrededor de 3.000 componentes en una semana”.
Evoluciona
“En términos de rendimiento, los meses de invierno son siempre duros”, explica Malcolm. “Es porque construímos piezas clave como montantes delanteros y traseros o los anclajes de la suspensión. Son cosas que posteriormente no tienes que hacer nuevamente hasta la siguiente temporada. Es entonces cuando entramos en ciclos de actualización trabajando más en los alerones delanteros y traseros, evoluciones del suelo o la construcción y reemplazo de partes caducadas por desgaste”.
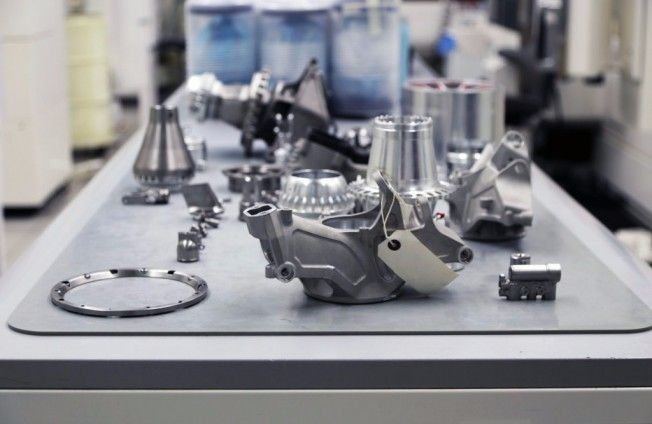
Malcolm y su equipo pueden empezar a respirar a mediado de febrero, pero eso no significa que lo más complicado haya pasado. “A mediados de febrero deberíamos empezar a relajarnos un poco. Han sido semanas de trabajo duro de cara a la presentación del coche y el primer test. Entonces disminuye de manera definitiva rumbo al inicio de la temporada. En este punto, nuestro enfoque se centra en entregar las actualizaciones necesarias para la temporada de competición”.
Todo está correcto
Pero siempre existen baches en el camino. La compleja mecanización de los componentes requerida para que una pieza sea estructural y aerodinámicamente correcta implica que el trabajo nunca es sencillo. Para Jones y su equipo, el trabajo más complejo del año es fabricar los montantes delantero y trasero: las intrincadas carcasas que unen la rueda, los componentes del freno y la suspensión. “Terminar los montantes delantero y trasero es definitivamente uno de los puntos álgidos de la temporada”, comenta. “Son los principales puntos de articulación de la suspensión y siempre hay mucha atención por parte de la empresa en esas piezas. Son aerodinámicas y estructurales y también necesitan aligerarse todo lo posible. Este año hemos prestado muchísima atención en el modo en que necesitábamos empaquetarlo, en el material necesario para ahorrar peso. Cada pieza nos lleva cerca de 30 horas y requiere cerca de ocho operaciones independientes”.
La temporada 2017 es especial en todos los sentidos y el programa habitual también debe cambiar para adaptarse a las circunstancias. “Realizamos diez sets de cuatro montantes y necesitamos al menos tres sets antes de la presentación. En esta época del año, normalmente hacemos los tres juegos iniciales, pero este año hemos fabricado todos. Es un reto realmente”.
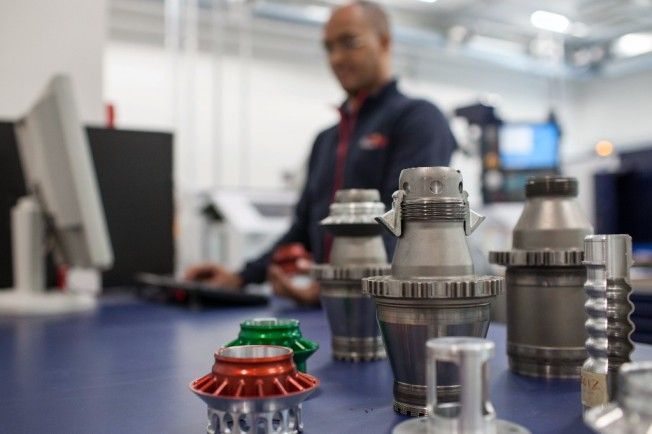
Las máquinas inteligentes no solo construyen mejores componentes, sino que simultáneamente incrementan el rendimiento y reducen el material desperdiciado. “Hemos hecho avances reales en materia de velocidad y eficiencia de nuestra producción. El software CAM nos permite arrastrar y soltar las secuencias en las máquinas mucho más fácilmente que antes y eso ha reducido el tiempo de producción. También hemos sido capaces de reducir el tiempo y material desechado de cada proceso, por lo que es muy útil”.
Girar la rueda
Un área en la que la maquinaria ha demostrado ser un jugador determinante es en la fabricación de las tuercas de las ruedas. McLaren Racing utiliza una máquina no tripulada que sólo se dedica a producir nuevas tuercas, mientras que con anterioridad se requerían tres o cuatro máquinas diferentes para completar el trabajo. Ahora, Malcolm y su equipo pueden dejar la máquina funcionando todo el día, liberando así carga de trabajo a otras tareas.
Del mismo modo, la nueva generación de máquinas (Mazak en el caso de McLaren) de cinco ejes implican que la mayoría de los trabajos pueden ser completados por una sola unidad, ya que tienen la agilidad necesaria para conseguirlo.
Junto con la mano de obra, la capacidad y agilidad de la maquinaria conseguida gracias a la experiencia, hacen que el taller de McLaren esté completamente preparado para preparar al MCL32 para su primera tentativa en la pista.
Fuente: McLaren F1Fotos: McLaren F1